Fabricated Keels
At MarsKeel Technology we produce a number of different combinations of materials and types of fabricated keel fins. The designs built are as diversified as the boats for which they are built, from fixed fins to hydraulically activated dagger board.
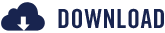
Download : Fabricated Fins Info Sheet
Read : Fabricated Fins Info Sheet
The range of combinations goes from a 400 lbs (182kg) Stainless Steel fin with a 1,100 lbs (455kg) bulb to a 7,650 lbs (3,477kg) mild steel fin with a 61,200 lbs (27,818kg) bulb. We have the ability to manufacture the keel fin from virtually any material that can be specified, or the North American equivalent, materials such as 316L to 2205 Duplex Stainless Steel to A514 or CHT 100 plate.
Fabrication Standards
All the fabrications are constructed by Canadian Welding Bureau Certified Welders, CSA Standard W47.1 Division 3, for fabrication in Steel, Stainless Steel, and Aluminum, using MIG, TIG and Stick. We maintain a staff to offer the customer a complete weld joint design and engineering, refer to the MarsKeel Design Group section of the website for more information.
Commonly Used Fabrication Materials (there are additions to this chart)
Material | Ultimate Tensile KSI | Ultimate Yeild KSI |
---|---|---|
Weldox 700 | 136 | 101 |
ASTM A514 | 110 | 100 |
304 SS | 75 | 30 |
316 SS | 75 | 30 |
Note: please note that these entries are for evaluation only, do not rely on them for engineering purposes.
Quality Assurance
Our dedication to quality begins with the third party confirmation that the raw material to be used is certified as acceptable before we even take possession of it from the suppliers. Generally for a fabricated fin this is the NDT and UT Certification of the raw material. The level of acceptability is based on the ASTM Standards. Other standards can be utilized as long as they are offered and all criteria are sent before the project production begins.
Design
The design range of the fins has gone from very simple designs with side shells with a welded on top and bottom plate (made from CHT 100) to very complicated internal webbing (made for attachment of lifting cylinders) with multi-part skins made from CNC pre-machined panels, all portions made from Weldox 900, 700, A514, Duplex 2205 SS, and 316L SS, then completely CNC machined if required. Please see our website section on Machined Keels for an explanation of the machining process.
Forming
Combined with the fabrication we offer a complete range of metal forming, bend forming, 6000 ton x 14′, plate rolling, 16′ x 22.5′. The quality of the technicians doing the forming is second to none. Their attention to detail allows the very highest level of accuracy in the fabrication shop.
Machining
Our complete machine shop can both post-machine any fabrication or pre-machine any part or assembly required by the fin or bulb. Everything from mounting plates to custom studs and custom nuts can be machined.
Finishing Process
The finishing process of the fins will consist of (depending on the material) the following steps:
- A surface preparation, media blasting.
- Self-etching primer is applied to the fin.
- Application of coats of Interprotect 2000E epoxy-based barrier coat, or similar product.
- Epoxy-based fairing, to a tolerance of less then 2mm. Our finishing technicians take great care to produce the best surface possible.
- Final application of the Interprotect 2000E epoxy barrier coat. There are more coats than required applied to allow for the final sanding without degrading coverage of barrier coat.
- Dry sand to remove orange peel. The surface is either dry or wet sanded to a maximum grit of Approx. 320
Bulb Production
The bulb production is very similar to the production process of a custom lead keel, offered on the Custom Keels – All Lead Keelspage.
The bulbs will utilize a combination of casting fixtures used to generate mounting and attachment systems for the fabricated fins. These systems can be as simple as a set of cast in keel bolts or as complicated as recesses and bolt holes.
We will generate the drawings for the required casting fixtures, based on the customer offered drawings. Therefore these parts are made under our direct oversight, with no oversight required by the designer or the builder.
The bulbs are generally attached to the fin by either horizontal or vertical bolting systems. Most of the bulb designs have incorporated a core into which the fin fits. We have the ability to produce virtually any shape or combination of core boxes and plunger rods to allow the attachment of the fin and the bulb. These parts can be fabricated or fully CNC machined to match necessary requirements.
Once the bulb is cast the fabricated fin and bulb are dry-fitted to ensure a proper engagement between them. All the recesses are accurate, the bolt holes line up and all the attachment parts will engage for the customer during final assembly.
Once our very skilled finishing department has completed the required finishing process for each part of the keel they are then released to the shipping staff. At this point the fin and bulb are loaded onto the custom designed and fabricated steel shipping cradle for loading into a sea container and delivered to the customer anywhere in the world.